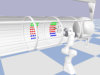
Girgin, H., Lembono, T.S., Cirligeanu, R. and Calinon, S. (2021)
Optimization of Robot Configurations for Motion Planning in Industrial Riveting
In Proc. IEEE Intl Conf. on Advanced Robotics (ICAR), pp. 247-252.
Abstract
Collaborative robots (cobots) have been increasingly used in the industry in recent years. The cobots are often 7-axis kinematically redundant manipulators. Exploiting these redundancies in industrial tasks is still a challenge as the change in the joint configuration of the robot can be unnecessarily large from one task to another depending on the initialization of the numerical inverse kinematics solution. In this article, we address this challenge in a particularly important under-explored industrial task: percussive riveting. The load exerted on the rivet for its plastic deformation can be dangerous for the robot if the natural frequency of the robot coincides with the frequency of the impact forces. In this work, we propose to take into account the vibrational characteristics of the manipulator to determine the robot joint configurations that minimize the overall end-effector's displacement. We also propose to exploit these safe joint configurations for each rivet hole in a task and motion planning algorithm called RoboTSP to generate the optimal trajectory visiting all target holes. We demonstrate our method with a Franka Emika Panda robot in a simulated environment.
Bibtex reference
@inproceedings{Girgin21ICAR, author="Girgin, H. and Lembono, T. S. and Cirligeanu, R. and Calinon, S.", title="Optimization of Robot Configurations for Motion Planning in Industrial Riveting", year="2021", booktitle="Proc.\ {IEEE} Intl Conf.\ on Advanced Robotics ({ICAR})", pages="247--252" }